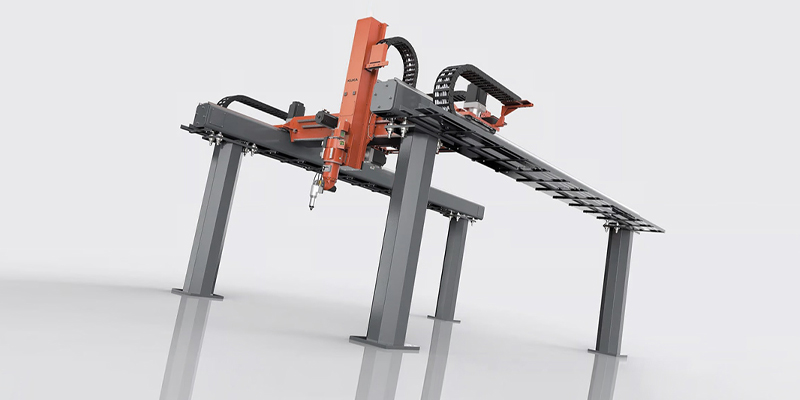
A gantry system is a motion-centric, multi-axis positioning apparatus characterized by an overhead bridge structure, designed to provide precise movement and manipulation within a defined workspace.
Typically employing Cartesian coordinates (X, Y, Z), these systems are widely utilized in industrial automation, manufacturing, and material handling applications for their ability to handle heavy loads and operate across large work envelopes with high accuracy and repeatability.
Industrial Versatility and Impact
Gantry systems have become indispensable in numerous industries due to their versatility, precision, and ability to handle large workspaces and heavy payloads. In the manufacturing sector, these systems play a crucial role in automating complex processes such as welding, machining, and assembly.
For instance, in automotive manufacturing, gantry robots can perform precise welding operations on large vehicle frames, significantly improving production speed and quality while reducing manual labor and associated risks.
The aerospace industry heavily relies on gantry systems for handling oversized components and performing intricate assembly tasks. These systems are particularly valuable when working with large aircraft parts that require precise positioning and manipulation across extensive work envelopes.
In the logistics and warehousing sector, gantry robots excel in material handling, sorting, and storage applications. Their ability to operate efficiently in large work areas makes them ideal for tasks such as palletizing, depalletizing, and automated storage and retrieval systems (AS/RS). This is especially important as e-commerce continues to grow, driving the need for more efficient and scalable warehouse automation solutions.
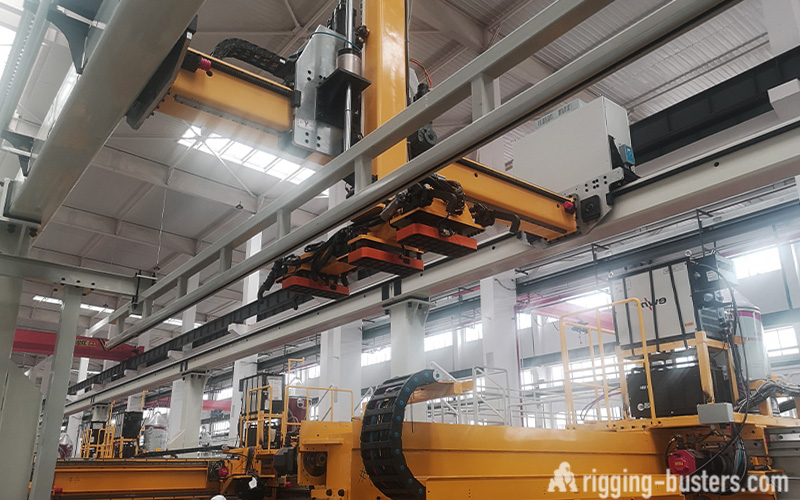
The food and beverage industry utilizes gantry systems for various applications, including packaging, sorting, and quality control. These systems can be designed to meet strict hygiene standards, making them suitable for handling food products in controlled environments.
In the metals and plastics industries, gantry robots are employed for heavy-duty material handling, cutting, and forming operations. Their robust construction and high payload capacity make them well-suited for manipulating large metal sheets or plastic components.
The paper industry benefits from gantry systems in applications such as roll handling, stacking, and packaging. These systems can efficiently manage large paper rolls and finished products, streamlining production and logistics processes.

Gantry robots also find applications in the construction industry, where they are used for automated bricklaying, 3D printing of buildings, and handling of prefabricated components. These applications demonstrate the potential of gantry systems to revolutionize traditional construction methods, improving efficiency and reducing labor costs.
The importance of gantry systems in these industries is further underscored by their ability to integrate with other automation technologies.
For example, they can be equipped with advanced vision systems for quality inspection or combined with conveyor systems for seamless material flow. This integration capability allows for the creation of highly efficient, automated production lines that can significantly enhance overall productivity and product quality.
Moreover, the scalability of gantry systems makes them particularly valuable as industries evolve and production requirements change. Their modular design allows for easy expansion or reconfiguration, providing businesses with the flexibility to adapt to new market demands or product lines. This adaptability is crucial in today’s fast-paced industrial landscape, where agility and responsiveness to market changes are key competitive advantages.
Core Structural Elements
Gantry systems are composed of several key components that work together to provide precise, multi-axis motion control. Here’s a detailed breakdown of these essential elements:
- Frame Structure:
- Typically consists of a main beam, end beams, support legs, and lower beams
- Can be box-shaped or truss-structured, depending on application requirements
- Provides stability and rigidity to support the entire system and its payload
- A-frame designs offer exceptional stability and load-bearing capacity
- T-frame configurations excel in confined spaces and minimize the system’s footprint
- Linear Rails and Guides:
- Form the backbone of the system, enabling smooth and precise movement
- Types include round, profiled, and V-shaped rails
- Selection depends on factors such as load capacity, speed, precision, and environmental conditions
- Profiled rails offer high precision and load-carrying capacity
- V-shaped rails provide a balance of rigidity and self-alignment
- Motors and Drives:
- Responsible for actuating the system’s motion
- Servo motors are commonly used for precise positioning
- Stepper motors may be employed in applications requiring less precision or lower costs
- Drives control the motors, interpreting signals from the control system
- End Effectors:
- Task-specific tools attached to the moving parts of the gantry
- Can include grippers, welding torches, cutting tools, or specialized instruments
- Designed to perform the intended operation on the workpiece or material
- Control System:
- Coordinates and manages all components to achieve desired motion and positioning
- Typically includes a programmable logic controller (PLC) or industrial computer
- Integrates with sensors for feedback and position monitoring
- May incorporate advanced features such as vision systems for quality inspection or process optimization
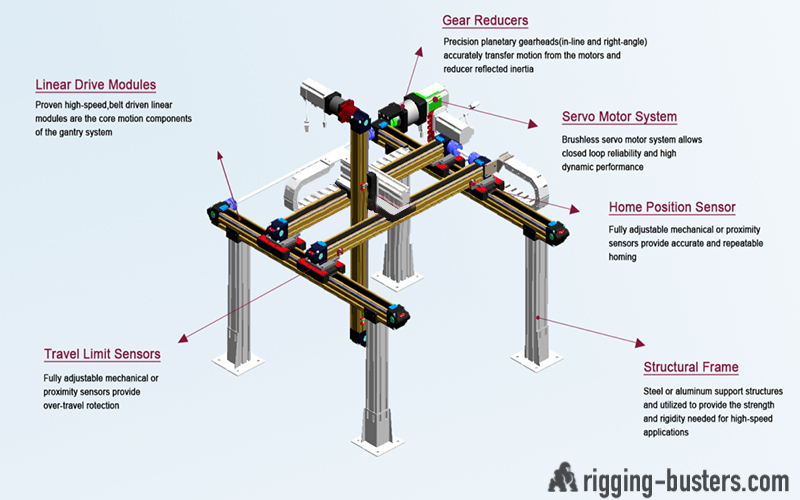
The integration of these components results in a highly versatile and efficient system capable of performing complex tasks across various industries. The modular nature of gantry systems allows for customization and scalability, adapting to specific application requirements and evolving production needs.
Gantry Kinematic Configurations
Gantry systems can be classified into three main types based on their coordinate systems and motion patterns:
- Cartesian Gantry Systems:
- Utilize three orthogonal axes (X, Y, Z) for linear motion
- Provide the largest work envelope and highest precision
- Ideal for applications requiring straight-line movements and rectangular work areas
- Commonly used in CNC machining, 3D printing, and pick-and-place operations
- Offer simple programming and intuitive control due to linear relationships between motor rotations and end effector position
- Polar Gantry Systems:
- Employ a combination of linear and rotary motions (R, θ, Z)
- Consist of a rotating base, an arm that extends radially, and a vertical axis
- Well-suited for circular or cylindrical work areas
- Efficient for operations within a circular workspace, such as semiconductor wafer handling or radial assembly tasks
- May require more complex motion control algorithms compared to Cartesian systems
- Cylindrical Gantry Systems:
- Combine linear and rotary motions (R, θ, Z) similar to polar systems, but with a fixed vertical axis
- Typically feature a rotating column with a horizontal arm that moves vertically and extends radially
- Excellent for applications involving tall, cylindrical work areas
- Commonly used in automated storage and retrieval systems (AS/RS) and vertical machining operations
- Offer a compromise between the work envelope of Cartesian systems and the rotary capabilities of polar systems

Each type of gantry system has its own advantages and limitations:
- Cartesian systems excel in applications requiring high precision and large rectangular work areas
- Polar systems are optimal for circular workspaces and can often achieve higher speeds in rotary motions
- Cylindrical systems combine aspects of both Cartesian and polar systems, making them versatile for a range of applications
The choice of gantry system type depends on factors such as:
- Required workspace geometry
- Precision and accuracy requirements
- Speed and acceleration needs
- Payload capacity
- Cost considerations
- Integration with existing infrastructure or processes
In some cases, hybrid gantry systems may be employed, combining elements of different types to meet specific application requirements. For example, a Cartesian-polar hybrid might use linear X and Y axes with a rotary Z axis for increased flexibility in certain operations.
Industrial Application Spectrum
Gantry systems find extensive applications across various industries due to their versatility, precision, and ability to handle large workspaces. The following table summarizes key applications of gantry systems in different sectors:
Application Area | Examples and Benefits |
---|---|
Manufacturing and Assembly | 🔹 Automotive assembly lines: Precise positioning of large components |
🔹 Aerospace: Handling oversized aircraft parts | |
🔹 Electronics: High-speed pick-and-place operations | |
Material Handling and Logistics | 🔸 Automated storage and retrieval systems (AS/RS) |
🔸 Palletizing and depalletizing in warehouses | |
🔸 Sorting and distribution in e-commerce fulfillment centers | |
Robotics and Automation | 🔹 Integration with industrial robots for extended reach |
🔹 Multi-axis motion control in automated production lines | |
🔹 Collaborative robot systems for human-robot interaction | |
CNC Machining and 3D Printing | 🔸 Large-scale additive manufacturing for construction |
🔸 Multi-axis CNC milling and cutting of oversized workpieces | |
🔸 Hybrid manufacturing combining additive and subtractive processes | |
Packaging and Palletizing | 🔹 High-speed packaging lines in food and beverage industry |
🔹 Case packing and carton erecting in consumer goods | |
🔹 Mixed-load palletizing for efficient logistics | |
Inspection and Quality Control | 🔸 Automated visual inspection systems |
🔸 Non-destructive testing of large components | |
🔸 Coordinate measuring machines (CMM) for metrology |
In manufacturing and assembly, gantry systems excel at handling heavy loads and large components with high precision. For instance, in automotive assembly lines, gantry robots can perform welding operations on vehicle frames, significantly improving production speed and quality. The aerospace industry utilizes gantry systems for manipulating oversized aircraft parts during assembly processes.

Material handling and logistics benefit from gantry systems’ ability to operate efficiently in large work areas. Automated storage and retrieval systems (AS/RS) employ gantry robots for high-density storage and rapid order fulfillment, crucial for e-commerce operations. These systems can handle a wide range of payloads, from small consumer goods to heavy industrial components.
In robotics and automation, gantry systems serve as a foundation for integrating various robotic technologies. They can extend the reach and workspace of industrial robots, enabling complex automation solutions. For example, a gantry-mounted robot arm can combine the precision of robotic manipulation with the large work envelope of a gantry system.
CNC machining and 3D printing applications leverage gantry systems for their ability to provide precise multi-axis motion control. Large-scale additive manufacturing, particularly in construction, uses gantry-based 3D printers to create building components or even entire structures. In traditional machining, gantry-based CNC mills can process oversized workpieces with high accuracy.
The packaging and palletizing industry employs gantry systems for their speed and flexibility. High-speed packaging lines in the food and beverage sector often utilize gantry robots for tasks such as case packing and palletizing. These systems can adapt to different package sizes and configurations, making them ideal for mixed-product handling.

In inspection and quality control, gantry systems provide a stable platform for various measurement and testing equipment. They can be equipped with vision systems, sensors, or coordinate measuring machine (CMM) heads to perform automated inspections of large or complex parts. This application is particularly valuable in industries with stringent quality requirements, such as aerospace and automotive manufacturing.
The versatility of gantry systems allows for their adaptation to emerging technologies and industry trends. For instance, they can be integrated with artificial intelligence and machine learning algorithms to optimize production processes, predictive maintenance, and quality control.
As industries continue to evolve towards smart manufacturing and Industry 4.0 principles, gantry systems are likely to play an increasingly important role in enabling flexible and efficient production environments.
Multifaceted Performance Attributes
Gantry systems offer numerous advantages that make them indispensable in various industrial applications. Here’s a detailed look at their key benefits:
- Versatility:
- Adaptable to diverse applications across industries
- Can be customized for specific production needs and layouts
- Capable of integrating various end-effectors for different tasks
- Suitable for both simple and complex motion patterns
- Precision:
- Operate on Cartesian coordinate systems, ensuring accurate 3D movements
- Can achieve positioning accuracy of ±0.5 µm or better
- Low angular deviation (±20 µrad) and excellent orthogonality (±25 µrad)
- Backlash-free operation for high bi-directional repeatability
- Scalability:
- Modular design allows for easy expansion or reconfiguration
- Can be adjusted to accommodate changing production requirements
- Stroke lengths can be customized to fit specific machine or workstation sizes
- Load capacity:
- Capable of handling heavy payloads due to robust frame structures
- Suitable for applications ranging from light assembly to heavy material handling
- Can be designed with pneumatic weight compensation for versatile tool handling
- Cost-effectiveness:
- Often more economical than 6-axis robots for certain applications
- Reduced need for manual labor in repetitive or hazardous tasks
- High throughput and productivity lead to improved ROI
- Lower complexity of mechanism enables rapid scaling and adaptation
- Additional advantages:
- High-speed operation (up to 1000 mm/s) and acceleration (15,000 mm/s²)
- Large work envelopes suitable for oversized components or extensive production lines
- Improved safety by keeping operators away from hazardous processes
- Ability to integrate with advanced control systems and software for optimized performance
These advantages make gantry systems particularly valuable in industries requiring high precision, flexibility, and efficiency in large-scale operations. Their ability to combine accuracy with scalability and cost-effectiveness positions them as a crucial technology in the ongoing evolution of industrial automation and smart manufacturing.
Gantry Design Optimization Parameters
When designing a gantry system, several critical factors must be carefully considered to ensure optimal performance and reliability. The following table summarizes key design considerations:
Design Consideration | Description and Importance |
---|---|
Load Capacity Requirements | 🔹 Determine maximum static and dynamic loads |
🔹 Consider safety factors (typically 1.5 to 2.5) | |
🔹 Account for payload, tooling, and acceleration forces | |
Speed and Acceleration Needs | 🔸 Define maximum speed (e.g., 1.28 m/s) and acceleration (e.g., 2.6G) |
🔸 Consider impact on precision and vibration | |
🔸 Evaluate motor and drive capabilities | |
Precision and Repeatability Requirements | 🔹 Specify required positioning accuracy (e.g., ±0.01 mm) |
🔹 Consider encoder resolution and mechanical tolerances | |
🔹 Evaluate need for error compensation techniques | |
Environmental Factors | 🔸 Assess temperature fluctuations and thermal expansion |
🔸 Consider dust, moisture, and corrosive elements | |
🔸 Evaluate electromagnetic interference sources | |
Integration with Existing Systems | 🔹 Ensure compatibility with control systems and software |
🔹 Consider interface requirements for end-effectors | |
🔹 Evaluate space constraints and mounting options |
Load capacity is a critical factor that influences component selection and overall system design. Engineers must calculate both static and dynamic loads, considering factors such as payload weight, tooling, and forces generated during acceleration and deceleration. A safety factor is typically applied to account for unforeseen forces and wear over time.
Speed and acceleration requirements significantly impact motor selection, drive capabilities, and mechanical component design.
High-speed operations may require specialized bearings and slides to minimize friction and heat generation. However, increasing speed and acceleration can introduce vibrations and reduce precision, necessitating careful optimization.
Precision and repeatability are crucial for many applications, particularly in industries like semiconductor manufacturing. High-resolution encoders, precision-ground linear guides, and rigid frame designs contribute to improved accuracy. Some systems may require error compensation techniques to achieve the desired precision.
Environmental factors can significantly affect gantry system performance. Temperature fluctuations can cause thermal expansion, impacting precision. Dust, moisture, and corrosive elements may necessitate specialized sealing and materials. Electromagnetic interference sources should be identified and mitigated to ensure reliable operation of sensors and control systems.
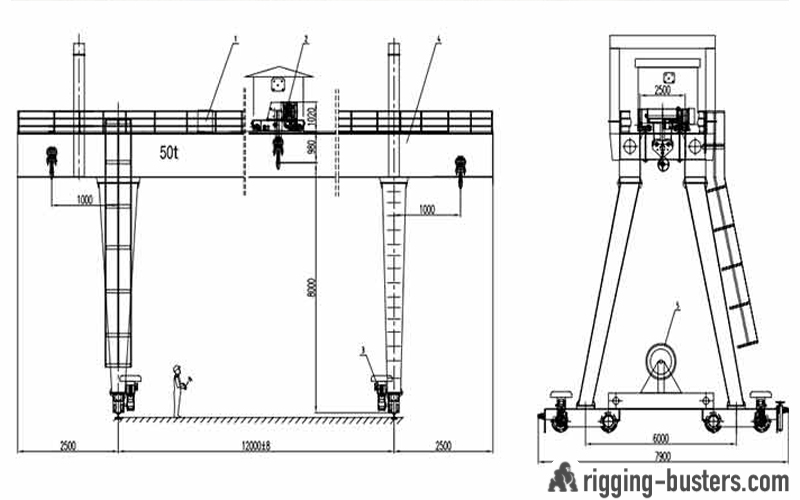
Integration with existing systems is a key consideration for many applications. The control system and software must be compatible with the gantry system’s requirements. For example, the Galil DMC-1842 motion controller mentioned in one application requires careful tuning of both velocity loops in the drives and position loops in the controller. Interface requirements for end-effectors and space constraints in the existing facility must also be evaluated.
When designing for high-speed operations, it’s important to consider the relationship between acceleration and cutting performance. For instance, in plasma cutting applications, an acceleration of about 35 IPS/sec (inches per second per second) is needed for speeds above 200 IPM (inches per minute) to achieve sharp corners and turns. This illustrates the intricate balance between speed, acceleration, and precision in gantry system design.
Advanced design techniques, such as S-curve profiling and acceleration feedforward, can be employed to optimize gantry performance. S-curve profiles minimize vibration by avoiding acceleration discontinuities, while acceleration feedforward improves tracking accuracy during acceleration and deceleration phases.
By carefully considering these design factors and employing advanced motion control techniques, engineers can create gantry systems that meet the specific requirements of their applications while maximizing performance, reliability, and efficiency.
Proactive Performance Optimization Protocols
Maintaining and optimizing gantry systems is crucial for ensuring long-term reliability, precision, and efficiency. A comprehensive maintenance strategy encompasses several key areas:
Regular Inspection and Maintenance:
- Conduct visual inspections of structural components, bearings, and drive systems at scheduled intervals
- Monitor key performance indicators such as positioning accuracy, repeatability, and vibration levels
- Implement predictive maintenance techniques using sensors and data analytics to detect potential issues before they lead to failures
- Perform non-destructive testing (NDT) on critical components to identify material fatigue or structural weaknesses
Cleaning and Lubrication:
- Develop a systematic cleaning schedule to remove debris, dust, and contaminants from linear guides, bearings, and other moving parts
- Use appropriate cleaning agents and methods based on the environmental conditions and materials involved
- Apply lubricants according to manufacturer specifications, considering factors such as load, speed, and operating temperature
- Implement automatic lubrication systems for high-duty cycle applications to ensure consistent lubrication and reduce maintenance downtime
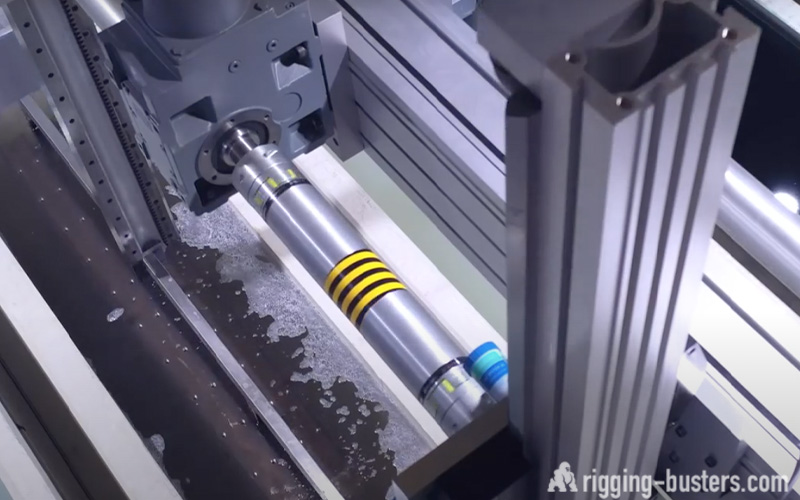
Alignment Adjustments:
- Regularly check and adjust the alignment of linear rails, bearings, and drive components
- Use precision measurement tools such as laser interferometers or electronic levels to verify alignment within specified tolerances
- Implement thermal compensation techniques to account for temperature-induced dimensional changes in large gantry systems
- Adjust preload on linear guides and bearings to optimize stiffness and minimize friction
Control System Updates:
- Periodically update control system firmware and software to incorporate the latest features and security patches
- Fine-tune control parameters such as PID gains, acceleration profiles, and error compensation tables to optimize performance
- Implement advanced control algorithms like Model Predictive Control (MPC) or Iterative Learning Control (ILC) for improved trajectory tracking and disturbance rejection
- Integrate condition monitoring and diagnostic capabilities into the control system for real-time performance analysis and fault detection
Optimization strategies for gantry systems often involve a combination of mechanical and control system enhancements:
- Utilize Finite Element Analysis (FEA) to identify and reinforce structural weak points, reducing vibration and improving dynamic performance
- Implement active vibration control techniques using piezoelectric actuators or inertial mass dampers for high-precision applications
- Optimize motion profiles using S-curve or jerk-limited trajectories to minimize vibration and improve settling time
- Employ feedforward control techniques such as acceleration feedforward to improve tracking accuracy during high-speed movements
For large-scale gantry systems, such as those used in additive manufacturing or aerospace applications, advanced optimization techniques may include:
- Multi-input multi-output (MIMO) control strategies to account for cross-coupling effects between axes
- Adaptive control algorithms that can adjust parameters in real-time based on changing payload or environmental conditions
- Model-based calibration procedures to compensate for geometric errors and thermal deformation across the entire work envelope
By implementing a comprehensive maintenance and optimization strategy, operators can significantly extend the lifespan of their gantry systems, improve productivity, and maintain high levels of precision and reliability throughout the system’s operational life.
Evolutionary Trajectories and Synthesis
The gantry system market is poised for significant growth and technological advancement in the coming years. Key trends shaping the future of gantry systems include:
Integration with Industrial Internet of Things (IIoT): Gantry robots are increasingly being connected to IIoT networks, enabling enhanced data collection, analysis, and real-time decision-making. This integration allows for improved efficiency, predictive maintenance, and optimization of production processes.
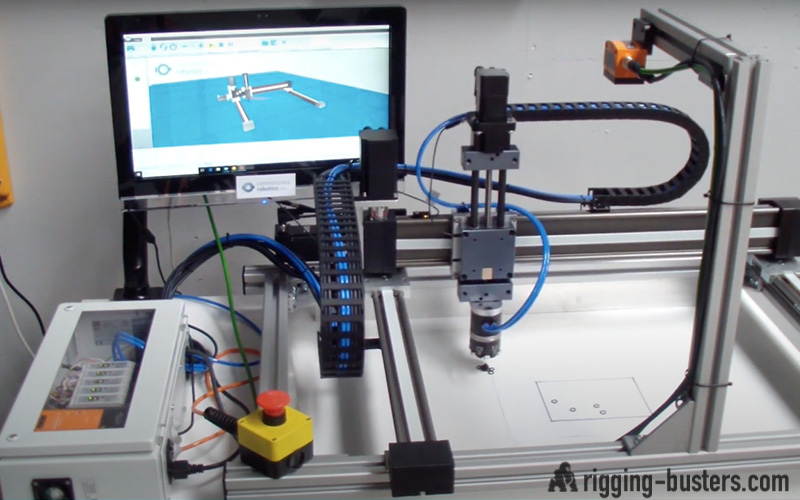
Advancements in AI and Self-Learning: Artificial intelligence is reaching new levels of sophistication in robotics, with a notable increase in self-learning gantry robots. These advanced systems can adapt to new tasks and environments, improving efficiency and reducing the need for constant human oversight.
Energy Efficiency and Sustainability: There is a growing emphasis on designing more energy-efficient and eco-friendly gantry systems. Manufacturers are focusing on using lightweight materials and optimizing robot movements to reduce power consumption, driven by both environmental concerns and the desire to lower operational costs.
Expansion of Gantry Robot Applications: The global gantry robot market is projected to grow at a CAGR of 8% from 2024 to 2031, indicating increasing adoption across various industries. This growth is driven by the versatility of gantry systems in applications such as material handling, welding, assembly, and inspection.
Enhanced User Interfaces: The development of more intuitive and user-friendly interfaces is making it easier for a broader range of workers to operate and interact with gantry systems. This evolution is reducing the barrier to entry and enhancing overall productivity.
Increased Adoption of Refurbished Robots: Companies are turning to refurbished gantry robots as a cost-effective solution, particularly for smaller enterprises. This trend not only reduces expenses but also promotes a more sustainable approach to industrial automation.
Advanced Control Systems: Future gantry systems are likely to incorporate more sophisticated control algorithms, such as Model Predictive Control (MPC) and Iterative Learning Control (ILC), to improve trajectory tracking and disturbance rejection. These advancements will lead to higher precision and efficiency in various applications.
Miniaturization and Modularization: As technology progresses, we can expect to see more compact and modular gantry designs. This trend will allow for greater flexibility in system configuration and easier integration into existing production lines.
Collaborative Gantry Systems: The development of collaborative gantry robots that can safely work alongside human operators is an emerging trend. These systems will combine the strength and reach of traditional gantry robots with advanced safety features and intuitive human-machine interfaces.
Integration with Additive Manufacturing: Gantry systems are playing an increasingly important role in large-scale additive manufacturing, particularly in the construction industry. Future developments may include more precise and faster 3D printing capabilities for building components or entire structures.
The gantry robot market is expected to grow from an estimated USD 3.99 billion in 2023 to USD 13.8 billion by 2032, exhibiting a CAGR of 14.78%. This substantial growth underscores the increasing importance and adoption of gantry systems across various industries.
As these trends continue to evolve, gantry systems will become more intelligent, efficient, and versatile, playing a crucial role in the ongoing industrial automation revolution and the realization of Industry 4.0 principles.
More useful info you can find 👉 here 👈