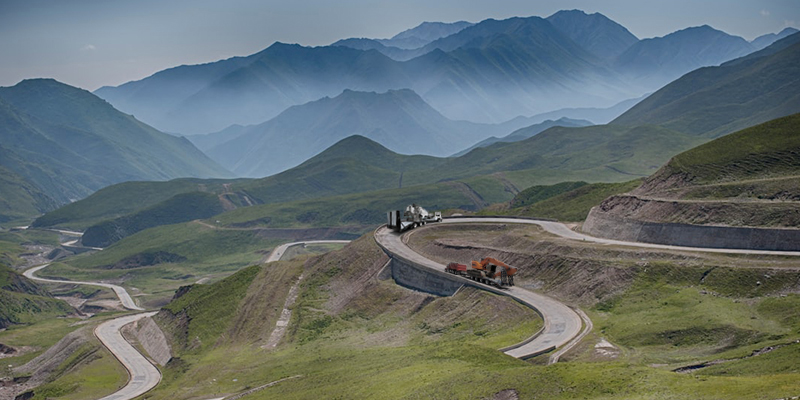
Moving heavy equipment and machinery is a complex task that requires careful planning, specialized tools, and strict adherence to safety regulations. This comprehensive guide covers the essential steps and best practices for transporting heavy machinery efficiently and safely, from conducting risk assessments to selecting the right equipment and securing loads properly.
Risk Assessment and Safety Protocols
Risk assessment is a critical step in ensuring the safe transportation of heavy equipment and machinery. Before moving any heavy loads, it’s essential to conduct a thorough risk assessment to identify potential hazards and implement appropriate control measures.
The risk assessment process involves several key steps:
- Identifying hazards: This includes examining the equipment, the route, and the loading/unloading areas for potential risks, such as unstable loads, overhead obstacles, or uneven terrain.
- Assessing risks: Evaluate the likelihood and severity of each identified hazard to determine the level of risk associated with the move.
- Implementing controls: Based on the risk assessment, put in place appropriate control measures to eliminate or minimize risks. This may include using specialized equipment, securing loads properly, or providing additional training to personnel.
- Reassessing risks: After implementing control measures, reassess the risks to ensure they have been effectively mitigated.
- Confirming reduced risk: Verify that the implemented controls have successfully reduced the risks to an acceptable level.
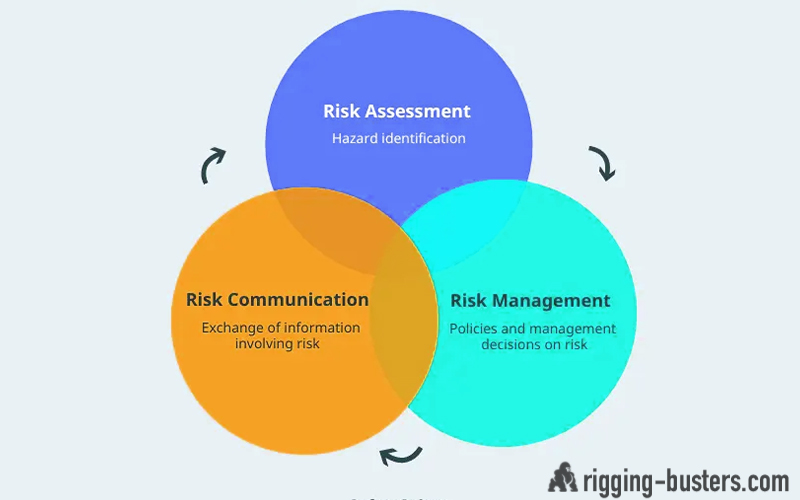
In addition to conducting risk assessments, it’s crucial to follow safety protocols throughout the moving process. This includes:
- Ensuring all personnel are properly trained and equipped with necessary personal protective equipment (PPE).
- Adhering to manufacturer guidelines and industry standards for loading, securing, and transporting heavy equipment.
- Regularly inspecting equipment, trailers, and tie-downs for any signs of wear, damage, or malfunction.
- Maintaining clear communication between all parties involved in the move, including drivers, loaders, and site supervisors.
By prioritizing risk assessment and safety protocols, companies can significantly reduce the likelihood of accidents, injuries, and equipment damage during the transportation of heavy machinery.
Choosing the Right Trailer and Hauler
When selecting the right trailer and hauler for transporting heavy equipment, it’s essential to consider several key factors to ensure safe and efficient transportation.
First, determine the weight and dimensions of the equipment being transported. This information will guide the selection of a trailer with the appropriate capacity and size to accommodate the load. Remember to account for the weight of the trailer itself when calculating the total weight the vehicle will be hauling. Trailers should also be low enough to meet the Federal Highway Administration’s (FHWA) minimum clearance height requirements of 14-16 feet on most interstates to safely pass under bridges and overpasses.
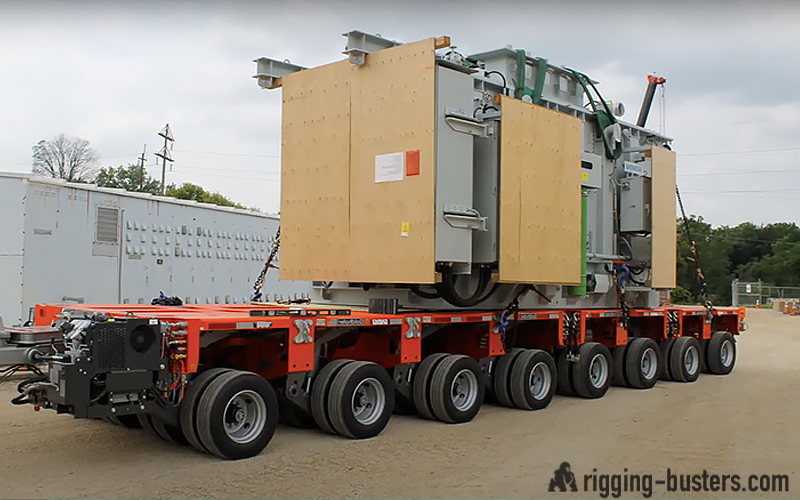
Next, evaluate the load distribution and center of gravity of the equipment. Proper placement of the machinery on the trailer is crucial for even weight distribution and stability during transport. Specialized trailers, such as lowboys, step decks, and extendable trailers, offer unique features and benefits for accommodating various equipment sizes, shapes, and loading requirements.
It’s also important to consider any special features or requirements of the equipment, such as fragile components or hazardous materials, which may necessitate specific trailer types or additional safety measures.
Before loading the equipment, inspect the trailer thoroughly for any signs of damage or weak points that could compromise the securement of the machinery. Ensure that the trailer is debris-free and that all tie-down points and securement devices are in good condition.
When it comes to selecting the right hauler, factors such as road regulations, permits, and route planning must be taken into account. Some oversized or overweight loads may require special permits and escort vehicles, which can impact transportation costs and logistics.
Working with a reputable heavy equipment transportation company can help navigate the complexities of regulations and safety requirements. Experienced professionals can provide valuable guidance in selecting the appropriate trailer and hauler, as well as ensuring proper loading, securement, and transportation procedures are followed.
By carefully considering equipment specifications, trailer features, road regulations, and safety requirements, you can choose the right trailer and hauler to ensure the safe and efficient transportation of your heavy equipment.
Securing Heavy Equipment: Best Practices
Properly securing heavy equipment is crucial for safe transportation and preventing accidents, injuries, or damage to the machinery. Follow these best practices to ensure your heavy equipment is secured correctly:
- Use appropriate tie-downs, such as chains, straps, or wire ropes, that are in good condition and have adequate working load limits for the equipment being transported. Chains are the preferred tie-down for heavy machinery.
- Whenever possible, use the equipment manufacturer’s designated attachment points and follow their securement recommendations. Each tie-down should be affixed as close as possible to the front and rear of the vehicle or to mounting points specifically designed for that purpose.
- Use direct tie-downs whenever possible, but keep in mind that they require the use of more tie-downs than indirect methods. Direct tie-downs provide a more secure connection between the equipment and the trailer.
- Ensure that the transport vehicle’s gross vehicle weight rating and/or gross combination weight rating will not be exceeded when the equipment is loaded. Overloading can lead to instability and increased risk of accidents.
- Place the equipment against a vehicle structure, such as a bulkhead or headboard, to help prevent forward movement during transport, unless weight distribution or securement considerations do not allow it.
- Use chocks, cradles, wedges, or other means to prevent rolling of wheeled equipment. These devices should be properly secured to the trailer deck.
- Lower all accessory equipment, such as booms, blades, or buckets, and secure them independently with separate tie-downs. This helps to stabilize the equipment and prevent damage to hydraulic systems.
- Apply the parking brake and place the transmission in the manufacturer’s recommended position for transport (e.g., neutral or park). This provides an additional layer of security against unintended movement.
- Inspect the equipment and securement devices periodically during transport, especially after sudden stops or rough road conditions, to ensure that the load remains properly secured. Make adjustments as necessary to maintain a safe and stable load.
By adhering to these best practices and following manufacturer guidelines, you can significantly reduce the risk of accidents and damage when transporting heavy equipment.
Identifying Potential Hazards
When working with heavy equipment, it is crucial to identify potential hazards to ensure the safety of operators, workers, and pedestrians. Some of the most common hazards associated with heavy machinery include:
- Moving parts and crush hazards: Heavy equipment often consists of large moving parts such as rotating blades, tracks, and conveyor belts, which can pose a significant crush hazard. Operators and workers must maintain a safe distance from these moving parts to avoid accidents.
- Falling objects and striking hazards: Improperly secured loads or unstable materials being lifted by heavy equipment can result in falling objects that pose a striking hazard. Operators and workers should wear appropriate personal protective equipment (PPE) and maintain a safe distance from the equipment during lifting and loading operations.
- Electrocution hazards: Heavy equipment can come into contact with power lines, leading to electrical shocks or electrocution. Operators should be aware of the risks associated with working near power lines, underground cables, or electrical installations. Insulated tools and proper training can help mitigate the risk of electrocution.
- Noise and vibration hazards: Prolonged exposure to the high levels of noise and vibrations generated by heavy equipment can lead to hearing loss, musculoskeletal disorders, and fatigue. Wearing hearing protection and taking regular breaks can mitigate these hazards.
- Fire and explosion hazards: Heavy equipment that operates with flammable fuels, hydraulic fluids, or lubricants poses a risk of fire or explosion. Routine inspections, proper storage of flammable substances, and adherence to safety protocols help prevent these incidents.
- Visibility hazards: Limited visibility from the operator’s cabin can lead to accidents. The use of mirrors and additional safety devices, along with proper positioning and signaling, improves visibility and reduces the risk of collisions.
- Rollovers and tip-overs: These accidents can occur when machinery is operated on uneven terrain, overloaded, or driven too fast. Proper training, regular inspections, and adherence to safe operating procedures can prevent rollovers and tip-overs.
- Struck-by and caught-in/between accidents: Workers close to heavy equipment are at risk of being run over, hit by moving parts, or trapped between the equipment and another object. Establishing designated work zones, wearing high-visibility clothing, and maintaining clear communication between operators and ground workers can minimize these risks.
By identifying and understanding these potential hazards, employers can implement effective control measures, provide comprehensive training, and foster a culture of safety when working with heavy equipment.
Weight Capacity Considerations
When transporting heavy equipment, it is essential to consider the weight capacity of the machinery, trailer, and hauler to ensure safe and efficient transportation. Here are some key points to keep in mind:
- Load capacity: Always refer to the manufacturer’s specifications and load capacity charts for the specific equipment you’re using. These documents provide precise information on safe load limits under various conditions. Exceeding the load capacity can lead to equipment failure, accidents, and even fatalities.
- Dynamic vs. static loads: Understand the difference between dynamic and static loads. Dynamic loads involve moving or shifting weights, which can stress equipment differently from static loads. Equipment should be rated for both types of loads.
- Gross vehicle weight rating (GVWR): Verify that the transport vehicle’s GVWR and/or gross combination weight rating (GCWR) will not be exceeded when the equipment is loaded. Overloading can lead to instability and increased risk of accidents.
- Weight distribution: Proper load distribution is crucial. Ensure that the weight is evenly distributed to prevent overloading one part of the equipment, which can lead to tipping or structural damage. Determine where the equipment will be placed on the transport vehicle to balance the weight distribution and secure the equipment properly.
- Tire pressure: If the equipment to be hauled has rubber tires, verify the tire pressure. Low pressure may result in the loosening of the tie-downs during transport.
- Accessory equipment: Consider the weight of any accessory equipment, such as attachments or counterweights, when calculating the total load weight. These additional components can significantly impact the overall weight and weight distribution of the load.
- Permits: Determine if permits for oversize or overweight movements will be required. These loads may also require warning flags, lights, and oversize load or wide load banners.
By carefully considering weight capacity and distribution, and adhering to manufacturer guidelines and regulations, you can ensure the safe and efficient transportation of heavy equipment.
Maintenance and Inspection Tips
Proper maintenance and inspection are crucial for ensuring the safe and efficient operation of heavy equipment. Here are some key tips for maintaining and inspecting heavy machinery:
Maintenance Tips | Inspection Tips |
---|---|
Follow the manufacturer’s recommended maintenance schedule for each piece of equipment. | Conduct visual inspections of the equipment before each use, checking for any signs of wear, damage, or leaks. |
Keep detailed records of all maintenance tasks performed, including the date, time, and any parts replaced or repaired. | Check fluid levels (e.g., oil, coolant, hydraulic fluid) and top up as needed. |
Lubricate moving parts regularly to reduce friction and wear, following the manufacturer’s guidelines for the type and amount of lubricant to use. | Inspect tires for proper inflation, tread wear, and any signs of damage or foreign objects. |
Replace filters (e.g., air, fuel, hydraulic) at the recommended intervals to maintain optimal performance and prevent contaminants from entering the system. | Test safety features, such as brakes, steering, and backup alarms, to ensure they are functioning properly. |
Clean the equipment regularly to remove dirt, debris, and corrosive materials that can accelerate wear and damage components. | Inspect hydraulic hoses and fittings for any signs of leaks, cracks, or wear, and replace as needed. |
By implementing a comprehensive maintenance and inspection program, you can:
- Extend the lifespan of your heavy equipment, reducing the need for costly repairs or replacements.
- Improve the reliability and performance of your machinery, minimizing unexpected breakdowns and downtime.
- Enhance safety by identifying and addressing potential hazards before they lead to accidents or injuries.
- Ensure compliance with industry regulations and standards, reducing the risk of fines or legal liabilities.
- Optimize fuel efficiency and reduce emissions by keeping equipment in peak operating condition.
Remember to train your operators and maintenance personnel on proper inspection and maintenance procedures, and foster a culture of proactive equipment care to maximize the benefits of your maintenance and inspection program.
Load Securing Techniques
Load securing is a critical aspect of safe and efficient transportation of heavy equipment and machinery. There are several techniques used to secure loads effectively, ensuring they remain stable during transit and minimizing the risk of accidents or damage. The two fundamental load securing methods are containment and restraint.
Containment involves limiting the loading area so that each item of freight rests against another item or the boundaries of the cargo area, such as the front wall, rear wall, or side walls, leaving no gaps. In practice, the cargo should be positioned tightly against these boundaries with minimal space between individual elements. However, some gaps are inevitable and must be filled or secured using restraints.
Restraint, on the other hand, relies on increasing the friction forces between the load and the loading surface. This is achieved by using lashing equipment to apply pressure on the load, pressing it more firmly onto the loading surface and preventing slippage. Friction alone keeps the load in place when using the restraint method.
Blocking and bracing is another common load securement method that utilizes lumber, metal bars, or plastic forms to inhibit the shifting of cargo in transit. These materials are positioned to fill voids and create a tight, secure arrangement of the load.
Dunnage, which includes materials like scrap wood, wooden boards, and specialized mechanical systems, is used to segregate cargo and prevent shifting in response to vehicle movements. Dunnage can be utilized to form cribs or provide additional blocking and bracing support.
Strapping, using materials such as steel or nonmetallic straps, is employed to unitize and secure loads. Straps are tensioned around the load to keep it tightly bound and prevent movement. Webbing straps made from synthetic fibers are also commonly used for load securement.
In some cases, specialized tarpaulins or nets are used to secure heavy, oddly-shaped objects like paper rolls. These materials can provide both containment and restraint by limiting horizontal movement and applying surface pressure when tensioned.
The most effective load securement often involves a combination of containment and restraint methods, as the elements of both techniques complement each other. The specific choice of load securing methods and materials depends on factors such as the type of cargo, transport vehicle, and regulatory requirements.
By employing appropriate load securing techniques and following industry guidelines and standards, transportation professionals can ensure the safe and efficient movement of heavy equipment and machinery, minimizing the risk of accidents, damage, and loss.
Personal Protective Equipment (PPE) Guidelines
Personal Protective Equipment (PPE) is essential for ensuring the safety of workers when handling heavy equipment and machinery. PPE acts as a barrier between the individual and potential hazards, minimizing the risk of injury or exposure to harmful substances.
When selecting PPE, it is crucial to choose equipment that meets relevant safety standards and is appropriate for the specific hazards present. Proper fit is also critical, as ill-fitting PPE may not provide adequate protection or could even create additional hazards.
Some key types of PPE for working with heavy equipment include:
- Head protection: Hard hats or helmets should be worn to protect against falling objects, overhead hazards, and potential head injuries.
- Eye and face protection: Safety glasses, goggles, or face shields are necessary to guard against flying debris, dust, splashes, or other eye hazards.
- Hearing protection: Earplugs or earmuffs should be used when working in noisy environments to prevent hearing damage.
- Respiratory protection: Respirators or masks may be required when working in areas with airborne contaminants, such as dust or fumes.
- Hand protection: Gloves should be worn to protect hands from cuts, abrasions, chemicals, or other hazards. The type of glove will depend on the specific hazard.
- Foot protection: Steel-toed boots or safety shoes can protect feet from crushing injuries, punctures, or slips.
- High-visibility clothing: Bright, reflective clothing helps increase worker visibility, especially in low-light conditions or when working near moving equipment.
Proper training on the use, maintenance, and limitations of PPE is essential for ensuring its effectiveness. Workers should be trained on how to correctly don and doff PPE, as well as how to inspect it for damage or wear.
Employers are responsible for providing appropriate PPE to their workers and ensuring that it is used correctly. They should also establish and enforce PPE policies and procedures, and regularly review and update their PPE program to address any changes in hazards or equipment.
By following these PPE guidelines and prioritizing worker safety, companies can significantly reduce the risk of injuries and illnesses associated with heavy equipment and machinery.
Emergency Response Procedures
Emergency response procedures are crucial for ensuring the safety of personnel and minimizing damage in the event of an accident or incident involving heavy equipment. Here is a table summarizing key emergency response steps:
Step | Description |
---|---|
Assess the situation | Quickly evaluate the nature and severity of the emergency, addressing any immediate life-threatening issues such as injuries, physical hazards, or environmental risks. |
Notify appropriate personnel | Contact the designated emergency response team, such as the Chief Warden or Building Security, and provide details about the incident. If necessary, call emergency services (e.g., fire department, ambulance) for assistance. |
Secure the area | Establish a perimeter around the incident site to prevent unauthorized access and further injuries. If possible, isolate or shut down the affected equipment. |
Evacuate personnel | If the situation warrants, evacuate all personnel to a designated assembly area, following established evacuation procedures and routes. Conduct a headcount to ensure everyone is accounted for. |
Administer first aid | If there are injuries, have trained first aid personnel assess and treat the injured until emergency medical services arrive. Retrieve first aid kits from designated locations. |
Control hazards | If safe to do so, take steps to control or mitigate any ongoing hazards, such as containing spills, extinguishing small fires, or stabilizing damaged equipment. |
Coordinate with emergency services | Upon arrival, brief emergency responders on the situation and provide any necessary information or assistance. Follow their instructions and cooperate fully with their response efforts. |
Investigate and document | Once the emergency is under control, conduct a thorough investigation to determine the cause of the incident and identify any corrective actions needed to prevent future occurrences. Document all aspects of the emergency response for reporting and record-keeping purposes. |
Effective emergency response relies on having well-developed and regularly practiced procedures in place. All personnel should be trained on their roles and responsibilities during an emergency, as well as familiar with evacuation routes, assembly areas, and communication protocols.
Emergency response plans should be tailored to the specific hazards and equipment present in each work environment, and should be reviewed and updated regularly to ensure they remain current and effective. By prioritizing emergency preparedness and following established response procedures, organizations can minimize the impact of accidents and incidents involving heavy equipment, and protect the safety and well-being of their personnel.
Calculating Load Limits
When transporting heavy equipment, it is crucial to calculate load limits accurately to ensure safe and efficient transportation. Load limits are determined by factors such as the equipment’s weight, the trailer’s capacity, and the hauler’s capabilities. Here’s a detailed explanation of how to calculate load limits:
- Working Load Limit (WLL): The WLL is the maximum load that a piece of equipment, such as a crane or rigging, can safely handle. It is calculated by dividing the Breaking Load Limit (BLL) by a safety factor (SF). For example, if a chain has a BLL of 2,000 lbs and a safety factor of 5, the WLL would be 400 lbs (2,000 lbs / 5 = 400 lbs).
- Load capacity: Always refer to the manufacturer’s specifications and load capacity charts for the specific equipment you’re using. These documents provide precise information on safe load limits under various conditions. Exceeding the load capacity can lead to equipment failure, accidents, and even fatalities.
- Gross Vehicle Weight Rating (GVWR): The GVWR is the maximum operating weight of a vehicle as specified by the manufacturer, including the vehicle’s chassis, body, engine, engine fluids, fuel, accessories, driver, passengers, and cargo. To calculate the load limit, subtract the weight of the passengers and cargo from the GVWR. For example, if a vehicle has a GVWR of 9,200 lbs and you estimate the weight of the driver, passengers, and cargo to be 1,200 lbs, the load carrying capacity would be 8,000 lbs (9,200 lbs – 1,200 lbs = 8,000 lbs).
- Load distribution: When calculating load limits, it’s important to consider the weight distribution on each axle or point of contact. Divide the total weight of the load by the number of contact points to determine the weight on each point. For example, if a 2,000 lb load is supported by 2 sling legs, each leg would bear 1,000 lbs (2,000 lbs / 2 legs = 1,000 lbs per leg).
- Safety margins: Always include a safety margin when calculating load limits to account for dynamic forces, such as wind, and other variables. Multiply the calculated weight per contact point by a load factor to determine the required capacity. Load factor tables are available for various sling angles. For example, a 60° sling angle has a load factor of 1.154, so the required sling capacity in the example above would be 2,308 lbs (1,000 lbs × 1.154 × 2 legs = 2,308 lbs).
By carefully calculating load limits using WLL, GVWR, load distribution, and safety margins, you can ensure that your heavy equipment is transported safely and efficiently without exceeding the capacity of the trailer, hauler, or rigging components. Always consult manufacturer specifications, industry standards, and relevant regulations to ensure compliance and safety when determining load limits.
Impact of Overloading
Overloading heavy equipment and vehicles can have severe consequences, compromising safety, performance, and longevity. When a vehicle is loaded beyond its designed capacity, it puts undue stress on various components, leading to accelerated wear and tear, reduced efficiency, and increased risk of accidents.
One of the most significant impacts of overloading is on the vehicle’s suspension system. Excess weight can cause the suspension to sag, reducing ground clearance and affecting handling. This not only makes the vehicle more difficult to control but also increases the likelihood of bottoming out on uneven surfaces, potentially causing damage to the undercarriage.
Overloading also puts additional strain on the vehicle’s brakes, reducing their effectiveness and increasing stopping distances. This is particularly dangerous when operating in challenging conditions or on steep inclines, as the brakes may not be able to generate sufficient force to slow down or stop the vehicle safely.

The vehicle’s tires are also susceptible to damage from overloading. Excess weight can cause tires to overheat, leading to increased wear and a higher risk of blowouts. Tire failure can result in loss of control, posing a serious safety hazard to the operator and nearby personnel.
Overloading can also lead to increased fuel consumption, as the engine must work harder to propel the additional weight. This not only increases operating costs but also results in higher emissions, contributing to environmental concerns.
In addition to the vehicle itself, overloading can cause damage to the infrastructure on which it operates. Overloaded vehicles place undue stress on roads, bridges, and other structures, accelerating deterioration and necessitating more frequent repairs. This can lead to increased maintenance costs and potential liability issues for operators and owners.
Moreover, overloading is often a violation of transportation regulations and can result in fines, penalties, and even the suspension of operating licenses. Overloaded vehicles may also be prohibited from accessing certain routes or facilities, limiting their operational flexibility.
To mitigate the risks associated with overloading, it is essential to adhere to the manufacturer’s specified load limits and follow proper loading techniques. This includes evenly distributing the load, securing it properly, and regularly inspecting the vehicle and its components for signs of wear or damage.
By understanding the severe consequences of overloading and taking proactive steps to prevent it, operators and owners can ensure the safe, efficient, and compliant operation of their heavy equipment and vehicles.
Signs of Overloading
Overloading heavy equipment and transport vehicles can lead to serious safety hazards and damage. It’s crucial to recognize the signs of overloading to prevent accidents and ensure safe transportation. Here are some common indicators that a vehicle or equipment may be overloaded:
- Sagging suspension: If the vehicle’s suspension appears to be sagging or sitting lower than normal, especially on one side, it may be a sign that the load is too heavy or unevenly distributed. This can cause handling issues and increase the risk of tire failure or structural damage.
- Difficulty steering or braking: Overloaded vehicles may exhibit reduced steering responsiveness or increased difficulty stopping. The extra weight can strain the vehicle’s braking system and make it harder to control, particularly on inclines or in emergency situations.
- Tire overheating or excessive wear: Overloading puts additional stress on tires, causing them to overheat and wear out more quickly. If tires are hot to the touch after driving, show signs of uneven wear, or experience frequent blowouts, it may indicate an overloaded condition.
- Unusual noises or vibrations: Overloaded vehicles may produce unusual noises, such as creaking, groaning, or banging sounds, from the suspension, frame, or other components. Excessive vibration or shaking can also be a sign of overloading, as the vehicle struggles to handle the additional weight.
- Reduced ground clearance: If the vehicle’s body appears to be sitting lower than usual or bottoming out on bumps or uneven surfaces, it may be overloaded. Reduced ground clearance can increase the risk of undercarriage damage and make it more difficult to navigate certain terrains.
- Strained engine performance: An overloaded vehicle may exhibit reduced engine performance, such as sluggish acceleration, difficulty maintaining speed on inclines, or increased fuel consumption. The engine has to work harder to propel the extra weight, leading to increased wear and reduced efficiency.
- Visible load shift or instability: If the load appears to be shifting, leaning, or otherwise unstable during transport, it may be a sign of improper loading or overloading. Uneven weight distribution can cause the vehicle to handle poorly and increase the risk of tipping or rollover accidents.
- Exceeded weight limits: Always check the gross vehicle weight rating (GVWR) and tire load ratings to ensure the vehicle and its components are not overloaded. If the total weight of the vehicle and its load exceeds these limits, it is a clear sign of overloading and poses significant safety risks.
By staying alert to these signs of overloading and taking prompt action to correct any issues, you can help prevent accidents, damage, and costly repairs. Regular vehicle inspections, proper load planning, and adherence to weight limits are essential for safe and efficient heavy equipment transportation.
Preventing Overload Damage
Here are some key strategies for preventing overload damage when transporting heavy equipment:
Use appropriate tie-downs and securement devices: Always use tie-downs, chains, straps, or other securement devices that are rated for the weight of the load and are in good condition. Ensure tie-downs are tightened properly to prevent the load from shifting during transport, which can cause overloading on certain points.
Distribute weight evenly: Properly distribute the weight of the equipment on the trailer to avoid overloading any one area. Place heavier items lower and closer to the center of the trailer. Uneven weight distribution can cause excessive stress on tires, suspension components, and the trailer structure itself.
Adhere to load capacity ratings: Never exceed the rated load capacity of the trailer, tow vehicle, or any securement equipment. Refer to the manufacturer’s specifications and gross vehicle weight rating (GVWR) to determine safe load limits. Overloading can lead to tire blowouts, suspension failure, and loss of vehicle control.
Inspect and maintain equipment regularly: Conduct thorough inspections of the trailer, tow vehicle, and all rigging components before each use. Look for signs of wear, damage, or excessive strain. Perform routine maintenance to ensure all equipment is in safe operating condition and able to handle the intended loads.
Plan routes carefully: Choose routes that avoid steep inclines, uneven surfaces, or other hazards that could exacerbate the effects of an overloaded trailer. Be aware of any weight restrictions or load limits on bridges or roads along the planned route.
Monitor load balance during transport: Periodically check the load balance and securement during transport, especially after sudden stops or rough road conditions. Adjust tie-downs or redistribute weight as necessary to maintain a stable, evenly-distributed load.
Use caution when loading and unloading: Exercise care when loading and unloading heavy equipment to prevent sudden shifts in weight distribution. Use proper lifting and rigging techniques, and ensure the loading surface is stable and level to avoid tipping or overloading.
By implementing these strategies and remaining vigilant about preventing overloading, you can significantly reduce the risk of damage to your heavy equipment, transport vehicles, and infrastructure. Always prioritize safety and compliance with load capacity guidelines to ensure successful and incident-free transportation.
Weight Distribution Strategies
When transporting heavy equipment, proper weight distribution is crucial for ensuring safe and stable transportation.

Here are some key strategies for optimizing weight distribution:
- Balance front-to-back: Distribute the weight evenly between the front and rear axles of the trailer. This helps prevent the trailer from tipping or swaying during transport. Ideally, aim for a balanced weight distribution where the front and rear axles carry the same amount of weight, as this improves traction, cornering, and braking.
- Distribute side-to-side: Similar to front-to-back balance, distributing weight evenly from side to side helps prevent swaying or tipping. Be mindful of this when loading asymmetrical equipment or when securing accessories like counterweights.
- Lower the center of gravity: Place heavier items lower on the trailer deck and closer to the centerline. This lowers the overall center of gravity, improving stability and reducing the risk of rollovers, especially when navigating turns or uneven terrain.
- Use proper tie-down points: Secure the load using the designated tie-down points on both the equipment and the trailer. This ensures that the weight is distributed as intended and prevents shifting during transport.
- Adjust for tongue weight: Ensure that the trailer tongue weight (the downward force exerted by the trailer on the hitch) is within the proper range, typically 10-15% of the total trailer weight. Too little tongue weight can cause trailer sway, while too much can overload the tow vehicle’s rear axle.
- Plan for axle weight limits: Be aware of the maximum weight limits for each axle on the tow vehicle and trailer. Distribute the load to stay within these limits, as overloading an axle can lead to tire failure, reduced braking performance, and other safety issues.
- Use load-leveling devices: If needed, use load-leveling hitches or air suspension systems to help distribute weight more evenly and maintain a level trailer. These devices can compensate for tongue weight and improve overall stability.
By implementing these weight distribution strategies, you can optimize the stability, safety, and performance of your heavy equipment transport. Always consult the equipment and trailer manufacturers’ guidelines, as well as relevant transportation regulations, to ensure compliance and safe operation.
Weather Impact on Transport
Weather conditions can have a significant impact on the safe transportation of heavy equipment. Extreme temperatures, wind, and precipitation can all pose challenges and risks that must be carefully considered and mitigated.
Cold weather can cause several issues for heavy equipment transport. Freezing temperatures can lead to the formation of ice on the equipment, trailer, and road surfaces, increasing the risk of slips, falls, and accidents. Cold weather can also cause hydraulic fluids and lubricants to thicken, potentially leading to reduced performance or equipment failure. To mitigate these risks, it’s important to properly winterize equipment, use appropriate fluids and lubricants for the temperature range, and take extra precautions when loading, unloading, and securing equipment in cold conditions.
Hot weather can also present challenges. High temperatures can cause equipment to overheat, leading to reduced performance or breakdowns. Extreme heat can also degrade tires, hoses, and other components more quickly. To combat these issues, it’s important to ensure that equipment cooling systems are functioning properly, to monitor equipment temperatures closely during transport, and to schedule transportation for cooler times of day when possible.
Wind can create significant hazards for heavy equipment transport, particularly for tall or top-heavy loads. Strong winds can cause trailers to sway or even tip over, and can make it difficult to control the vehicle. Gusty conditions can also cause unsecured equipment or accessories to shift or become dislodged. To reduce wind-related risks, it’s crucial to properly secure all equipment and accessories, to monitor wind conditions along the planned route, and to adjust driving techniques or even delay transportation in severe wind conditions.
Precipitation, such as rain, snow, or ice, can create slippery road conditions that make it more difficult to control the vehicle and increase stopping distances. Wet conditions can also reduce visibility and increase the risk of hydroplaning. In snowy or icy conditions, the accumulation of snow or ice on the equipment and trailer can add significant weight and alter the load distribution, affecting stability and handling. To minimize precipitation-related risks, it’s important to ensure that the vehicle and trailer are equipped with appropriate tires and brakes for the conditions, to reduce speed and increase following distances, and to frequently clear snow and ice accumulation from the equipment and trailer.
By understanding the potential impacts of various weather conditions on heavy equipment transport and taking appropriate precautions, transportation professionals can significantly reduce the risks associated with extreme temperatures, wind, and precipitation.
Careful planning, regular equipment maintenance, and adherence to best practices for loading, securing, and transporting equipment can help ensure safe and successful transportation even in challenging weather conditions.
Legal Compliance and Permits
Legal compliance and obtaining necessary permits are critical aspects of transporting heavy equipment safely and efficiently. Companies must adhere to various laws, regulations, and industry standards to ensure the lawful operation of their vehicles and equipment.
Legal compliance involves following all applicable federal, state, and local laws related to the transportation of heavy machinery. This includes requirements for vehicle registration, insurance, driver licensing, and compliance with weight and size limits. Companies must also adhere to regulations governing the safe operation of vehicles, such as hours-of-service rules for drivers and maintenance standards for equipment.
Obtaining the necessary permits is another crucial aspect of legal compliance. Depending on the type of equipment being transported and the route taken, companies may need to secure special permits for oversized or overweight loads. These permits typically specify the allowable dimensions, weight, and configuration of the load, as well as any restrictions on travel times or routes.
To obtain the required permits, companies must provide detailed information about the equipment being transported, including its make, model, dimensions, and weight. They may also need to submit a proposed route plan and demonstrate that the vehicle and load meet all applicable safety standards.
Failing to comply with legal requirements or obtain necessary permits can result in significant penalties, including fines, vehicle impoundment, and even criminal charges in severe cases. Non-compliance can also lead to accidents, damage to infrastructure, and harm to public safety. To ensure legal compliance and proper permitting, companies should:
- Understand and stay current on all relevant laws, regulations, and industry standards.
- Develop and implement policies and procedures to ensure compliance at all levels of the organization.
- Provide thorough training to employees on legal requirements and permit processes.
- Conduct regular audits and inspections to identify and address any compliance issues.
- Work closely with permitting authorities to ensure that all necessary permits are obtained in a timely manner.
By prioritizing legal compliance and proper permitting, companies can avoid costly penalties, protect public safety, and ensure the smooth and efficient transportation of their heavy equipment.
Training and Compliance Requirements
Training and compliance requirements are essential for ensuring the safe and legal operation of heavy equipment. Employers must provide comprehensive training to their employees and adhere to various regulations and industry standards.
Compliance training educates employees about the laws and regulations applicable to their job functions and industry. This training is often mandated by legislation, regulation, or company policy. The specific compliance topics covered will vary depending on the industry, activities, and location, but may include:
- Anti-harassment and diversity training to promote a respectful workplace
- Privacy training on safely handling personal or sensitive information
- Occupational health and safety training to comply with workplace safety standards
- Industry-specific regulatory compliance, such as OSHA standards for hazardous jobs or FAA requirements for aviation safety
In addition to mandatory compliance training, employers should provide thorough operational and safety training for employees working with heavy equipment. This includes:
- Hands-on training on the proper use, maintenance, and inspection of specific equipment
- Instruction on identifying and mitigating potential hazards associated with the machinery and work environment
- Emergency response procedures and protocols for accidents or equipment failures
- Training on proper loading, securing, and transporting techniques for heavy equipment
To implement an effective compliance and safety training program, employers should:
- Identify the specific training requirements based on applicable laws, regulations, and company policies
- Develop comprehensive training content that covers all necessary topics and procedures
- Utilize engaging training methods, such as hands-on demonstrations, simulations, and real-world scenarios
- Establish clear timelines and deadlines for completing required training, typically upon hiring and at regular intervals thereafter
- Maintain detailed records of each employee’s training completions to demonstrate compliance
- Regularly review and update training programs to ensure they remain current and effective
By investing in robust compliance and safety training, employers can foster a culture of safety, reduce the risk of accidents and legal liabilities, and ensure that their employees have the knowledge and skills necessary to operate heavy equipment safely and efficiently.
More useful info you can find 👉 here 👈