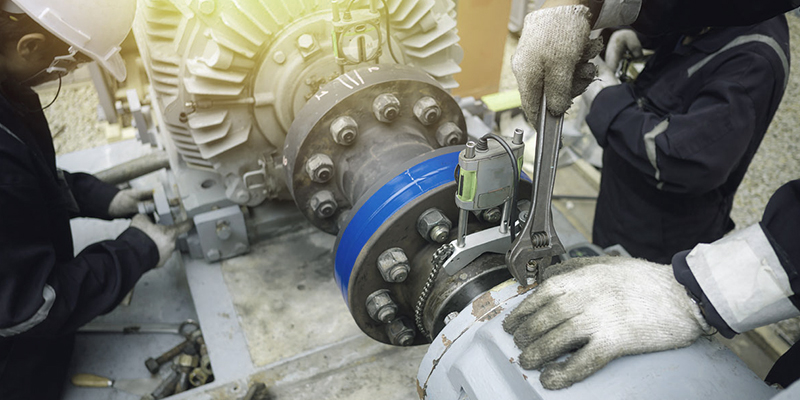
Millwright services are crucial for ensuring the smooth operation and longevity of industrial machinery. While often confused with mechanics, millwrights specialize in the installation, maintenance, repair, and precision alignment of complex equipment, making them essential partners for industries ranging from manufacturing to energy production.
Historical Evolution of Millwright Services
The millwright profession has undergone significant changes throughout history, evolving from a highly specialized and versatile role in the pre-industrial era to a more focused and technical occupation in modern times.
In the 17th and 18th centuries, millwrights were master craftsmen who designed and constructed entire mills, including the water wheel systems, gear mechanisms, and mill machines. They possessed a wide range of skills, combining elements of carpentry, blacksmithing, and masonry. Millwrights of this era were also proficient in arithmetic and geometry, enabling them to calculate velocities, strength, and power of machines, as well as design buildings and watercourses.

As the Industrial Revolution progressed in the late 18th and early 19th centuries, the role of the millwright began to change. The introduction of the steam engine and the rise of powered textile mills required millwrights to adapt their skills to new technologies. They were instrumental in building and maintaining the first factories, but their all-encompassing role started to fragment into more specialized trades, such as turners, fitters, machine makers, and mechanical engineers.
In the late 19th century, the increasing use of iron and steel in industrial machinery further transformed the millwright’s trade. They now worked primarily with metal instead of wood and were responsible for executing plans produced by designing engineers, rather than planning and designing machines themselves. Millwrights of this era required a strong technical education, as they had to calculate the strength of materials, read drawings, understand electricity, and build with metal.
Today, millwrights are highly skilled craftsmen who specialize in the precision-fitting, installation, and alignment of heavy industrial machinery. They work with a wide range of equipment, including conveyor systems, electric generators, and even complex machines in the nuclear industry. Modern millwrights must maintain tolerances of a thousandth of an inch and ensure the efficient operation of the machinery they install and maintain.
Despite the evolution of their role, millwrights remain essential to various sectors, including manufacturing, construction, and power generation. Their expertise in installing, maintaining, and repairing industrial equipment makes them indispensable for ensuring the smooth operation and longevity of machinery in these industries.
Early Millwright Innovations
Early millwrights were responsible for several significant innovations that greatly impacted the development of mills and industrial machinery. Some of their most notable contributions include:
Waterwheel and toothed gearing: In the Hellenistic period, Greek millwrights invented the two main components of watermills – the waterwheel and toothed gearing. These innovations allowed for the efficient harnessing of waterpower and laid the foundation for future mill designs.
Undershot, overshot, and breastshot waterwheels: Greek and Roman millwrights were the first to operate undershot, overshot, and breastshot waterwheel mills. These different wheel configurations allowed mills to be adapted to various water sources and flow conditions, increasing their versatility and efficiency.
Shipmill: Muslim millwrights developed the shipmill, a type of watermill powered by water wheels mounted on the sides of ships moored in midstream. This innovation allowed mills to take advantage of increased water flow without the need for permanent structures.
Industrial mills in Medieval Europe: In Medieval Europe, millwrights built the first industrial mills, which introduced new and innovative uses of waterpower. These mills played a crucial role in the growth of various industries, such as textile production and metallurgy.
Substitution of iron for wood: As the iron industry improved in the early 19th century, millwrights began using more cast iron components in mill construction. This shift from wood to iron allowed for the creation of more precise, durable, and efficient machinery.
Smock mill with fantail: In the 19th century, millwrights developed the smock mill, a type of windmill that used a fantail – a small wind-wheel set at a right angle to the sails – to automatically turn the cap of the windmill to face the wind. This innovation replaced the manual tailpole and improved the efficiency of windmills.
These early innovations by millwrights laid the groundwork for the mechanization of various industries and paved the way for the Industrial Revolution. By continually adapting to new technologies and materials, millwrights played a vital role in the advancement of manufacturing and power generation throughout history.

Key Skills and Training for Millwrights
Millwrights require a diverse set of skills and extensive training to excel in their profession. A strong foundation in mechanical aptitude and problem-solving is essential, as millwrights must be able to read blueprints, interpret schematics, and troubleshoot complex machinery.
Key hard skills for millwrights include proficiency with hand tools, hoists, cranes, and other equipment used for dismantling, installing, and maintaining industrial machinery. They must be skilled in preventative maintenance, conveyor systems, hydraulic systems, and mechanical and pneumatic systems. Welding, including MIG, arc welding, and the use of cutting torches, is another crucial skill for millwrights.
In addition to these technical skills, millwrights must possess important soft skills such as a strong work ethic, attention to detail, and the ability to work well in a team. They must be able to communicate effectively and adapt to various work environments, as their job often requires travel to different industrial sites.
To acquire these skills, aspiring millwrights typically complete a comprehensive apprenticeship program lasting three to four years. These programs combine on-the-job training with classroom instruction, covering topics such as mechanical systems, electrical systems, machine shop practices, and energy conservation. Apprentices must complete a minimum of 1,560 hours of on-the-job training annually, working under the guidance of experienced millwrights.

Upon completion of the apprenticeship, millwrights must pass an interprovincial exam to earn their Red Seal certification, which is recognized across Canada. Some provinces, such as British Columbia and Saskatchewan, also require millwrights to obtain additional certifications from their respective trade authorities.
Continuous learning and skill development are essential for millwrights to stay current with evolving technologies and industry practices. Many pursue additional training in specialized areas such as robotics, programmable logic controllers (PLCs), and predictive maintenance techniques to enhance their expertise and career prospects.
Comparing Millwrights and Industrial Mechanics
While millwrights and industrial mechanics share some similarities, there are key differences in their roles and responsibilities:
- Millwrights have a broader scope of work, which includes installing, maintaining, repairing, and transporting heavy machinery and equipment, while industrial mechanics primarily focus on maintenance and repair.
- Millwrights are highly skilled in precision-fitting, installing, and aligning complex industrial machinery, such as conveyor systems, turbines, generators, and hydraulic equipment. They ensure that machines are installed and assembled to exact specifications and tolerances.
- Industrial mechanics specialize in maintaining and repairing already installed machinery to keep it running at optimal levels. They perform regular maintenance, diagnose issues, and make repairs to prevent breakdowns and improve efficiency.
- Millwrights often work on a project basis, traveling to different industrial sites to install or dismantle machinery, while industrial mechanics are typically employed full-time by a single company to maintain their equipment on a daily basis.
- Millwrights require more extensive training, often completing a 3-5 year apprenticeship program that combines on-the-job training with classroom instruction. Industrial mechanics may attend technical school but do not typically require an apprenticeship.
- Due to their broader skill set, millwrights can often perform the tasks of an industrial mechanic, but the reverse is not always true. Millwrights are equipped to handle more complex installations, major repairs, and equipment relocations that may be beyond the scope of an industrial mechanic.

In summary, while both millwrights and industrial mechanics are essential for maintaining and repairing industrial equipment, millwrights have a more comprehensive role that includes installation, relocation, and major overhauls, while industrial mechanics focus on day-to-day maintenance and repairs to keep machinery running smoothly.
Career Path Differences
Millwrights and industrial mechanics have distinct career paths, with differences in education, training, and job responsibilities:
- Millwrights typically complete a comprehensive 3-5 year apprenticeship program that combines on-the-job training with classroom instruction, while industrial mechanics may attend technical school but do not usually require an apprenticeship.
- Millwrights often earn a degree from a technical school in addition to their apprenticeship, whereas becoming an industrial mechanic doesn’t necessarily require a technical degree.
- Millwrights must pass an interprovincial exam to earn their Red Seal certification, which is recognized across Canada, and some provinces require additional certifications from their respective trade authorities. Industrial mechanics do not have these certification requirements.
- Millwrights have a broader scope of work that includes installing, maintaining, repairing, and transporting heavy machinery, while industrial mechanics primarily focus on maintenance and repair of already installed equipment.
- Millwrights often work on a project basis, traveling to different industrial sites for installations or major repairs, whereas industrial mechanics are typically employed full-time by a single company to handle day-to-day maintenance.
- Due to their more extensive training and diverse skill set, millwrights can advance to roles such as project managers, supervisors, or even start their own contracting businesses. Industrial mechanics may have more limited advancement opportunities within their specific industry.
- The median annual wage for millwrights was $60,330 in May 2021, slightly higher than the $59,840 median wage for industrial machinery mechanics. However, actual salaries can vary based on factors like industry, location, and experience.

In summary, while both millwrights and industrial mechanics play vital roles in maintaining industrial equipment, millwrights have a more comprehensive career path that involves extensive training, diverse job responsibilities, and greater opportunities for advancement and entrepreneurship.
Critical Skills for Millwrights
Millwrights require a diverse set of technical and interpersonal skills to excel in their profession.

Some of the most critical skills for millwrights include:
Mechanical aptitude: Millwrights must have a strong understanding of mechanical concepts and be able to read and analyze blueprints, schematics, and technical manuals to troubleshoot and solve problems. They should be proficient in using a wide range of hand and power tools to perform maintenance and repairs on various types of machinery.
Welding: Welding is a crucial skill for millwrights as it enables the fabrication, repair, and maintenance of machinery and structural components, ensuring their durability, reliability, and alignment within various industrial settings.
Precision alignment: Millwrights must be skilled in precision alignment techniques, such as laser alignment, to ensure that machinery is installed and assembled to exact specifications and tolerances. This is critical for preventing premature wear, reducing vibration, and optimizing equipment performance.
Problem-solving: Strong problem-solving skills are essential for millwrights, as they must be able to analyze complex systems, identify the root cause of issues, and develop effective solutions. They need to think critically and creatively to address unique challenges that arise in their work.
Physical fitness: Millwrights often work in physically demanding environments, requiring them to lift heavy equipment, work in awkward positions, and stand for extended periods. They must have the strength, stamina, and dexterity to perform their tasks safely and efficiently.
Communication: Effective communication is crucial for millwrights, as they often work as part of a team and must collaborate with other tradespeople, such as electricians and welders. They should be able to clearly convey information, listen actively, and provide updates on project progress to clients and supervisors.
Safety awareness: Millwrights work with heavy machinery and equipment, making safety awareness a top priority. They must have a thorough understanding of safety protocols, be able to identify potential hazards, and take appropriate measures to prevent accidents and injuries.
Continuous learning: As technology and industry practices evolve, millwrights must commit to continuous learning and skill development. Staying updated with the latest techniques, tools, and safety standards is essential for remaining competitive and delivering high-quality work.
By mastering these critical skills, millwrights can effectively install, maintain, and repair a wide range of industrial machinery, ensuring optimal performance and longevity for the equipment they work on.
Precision Alignment Techniques
Precision alignment is a critical technique used by millwrights to ensure that industrial machinery operates efficiently and reliably. By accurately aligning equipment components, millwrights can prevent premature wear, reduce vibration, and optimize overall performance.
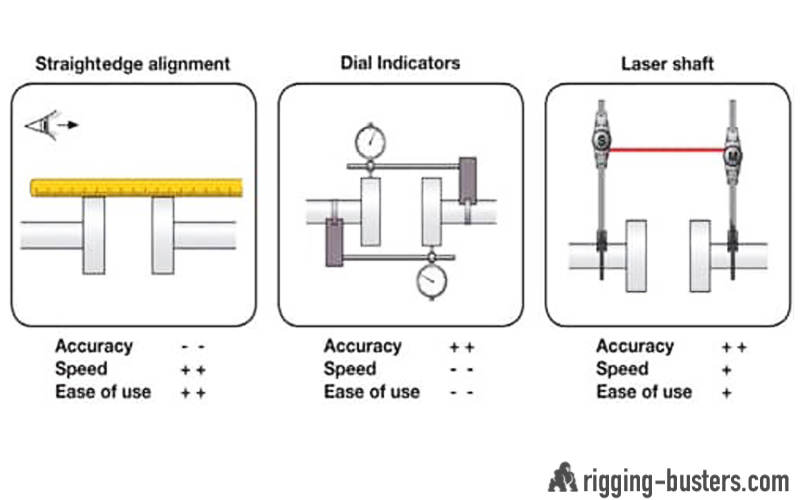
Here are some key precision alignment techniques used in the field:
Technique | Description |
---|---|
Reverse Dial Indicator Method | This method uses dial indicators to measure the relative positions of two machine shafts. By taking readings at various positions and performing calculations, millwrights can determine the necessary adjustments to achieve proper alignment. |
Laser Alignment | Laser alignment systems use laser transmitters and receivers to measure the straightness, flatness, and parallelism of machine components. This advanced technology provides highly accurate readings and allows for real-time adjustments during the alignment process. |
Graphical Alignment Techniques | Millwrights use graphical methods, such as plotting alignment data on specially designed graph paper, to visualize misalignment and determine the required corrections. This approach helps reinforce basic alignment concepts and enables millwrights to “see” the adjustments needed. |
Thermal Growth Compensation | Machinery components can expand or contract due to temperature changes, affecting alignment. Millwrights must account for thermal growth by taking measurements at different operating temperatures and making corresponding adjustments to ensure proper alignment under all conditions. |
Shaft Alignment | Precise shaft alignment is essential for the smooth operation of rotating equipment like pumps, motors, and gearboxes. Millwrights use tools like dial indicators, laser systems, and shims to align shafts within specified tolerances, often as tight as 0.001 inches. |
In addition to these techniques, millwrights must also consider factors such as machine soft foot (uneven base), pipe strain, and foundation settlement when performing precision alignment. They must follow proper procedures for taking accurate measurements, making adjustments, and documenting the alignment process for future reference.
By mastering these precision alignment techniques and tools, millwrights can ensure that industrial machinery operates at peak efficiency, minimizes energy consumption, and experiences fewer breakdowns. This expertise is critical for industries ranging from manufacturing to power generation, where equipment reliability and performance are paramount.
Specialized Tools and Techniques
Millwrights rely on a variety of specialized tools and techniques to perform their work effectively. These tools and methods enable them to install, maintain, and repair complex industrial machinery with precision and efficiency.
- Alignment tools: Millwrights use advanced alignment tools, such as laser alignment systems, dial indicators, and surface plates, to ensure that machinery components are precisely aligned. Proper alignment is critical for preventing excessive vibration, wear, and premature failure of equipment like pumps, motors, and conveyors.
- Rigging and hoisting equipment: Millwrights utilize rigging and hoisting equipment, including chains, ropes, slings, shackles, and pulleys, to safely lift, move, and position heavy machinery during installation and maintenance. Proper use of this equipment requires careful planning and adherence to strict safety protocols to prevent accidents and damage to the machinery.
- 3D printing and additive manufacturing: Modern millwrights are increasingly using 3D printing and additive manufacturing technologies to create custom parts on-site with high precision. This eliminates the need to wait for parts from manufacturers, reducing downtime and allowing for faster completion of jobs. 3D printing also enables the creation of complex parts that may have been previously unavailable or infeasible.
- Robotics: Millwrights are employing robotics to enhance safety and precision in hazardous tasks that would otherwise be performed manually or require multiple people. Robotics allow for more accurate measurements and improved efficiency in various projects.
- Advanced computing software: Millwrights use advanced computing software, such as CAD/CAM programs, to visualize and plan machinery installations and repairs before starting the actual work. These programs provide detailed models and reports on machine functioning, potential malfunctions, and optimization opportunities, saving time and money in the process.
- Welding and cutting equipment: Welding and cutting tools, such as MIG welders, arc welders, and cutting torches, are essential for millwrights to fabricate, modify, and repair industrial equipment. Proficiency in various welding techniques allows millwrights to work with different materials and machinery components.
By leveraging these specialized tools and techniques, millwrights can tackle complex industrial projects with greater accuracy, efficiency, and safety, ultimately ensuring the optimal performance and longevity of the machinery they install and maintain.
Laser Alignment Tools
Laser alignment tools are essential for millwrights to ensure precise alignment of rotating machinery shafts. These advanced tools enable efficient and accurate alignment, reducing vibration, preventing premature wear, and optimizing equipment performance.

Here are some key points about laser alignment tools:
- Laser shaft alignment systems are the most efficient way to align rotating machinery shafts, saving time and money compared to conventional alignment methods. They allow millwrights to quickly perform precision shaft alignments on most rotating machines in industrial plants.
- Leading laser alignment tool manufacturers include Easy-Laser, Fluke, and Prüftechnik (part of Fluke Reliability). These companies offer a range of laser alignment systems designed for different applications and user skill levels.
- Advanced laser alignment systems like the Easy-Laser XT770 enable millwrights to perform shaft alignment on horizontal and vertical/flange-mounted machines, align machine trains, measure straightness and flatness, and assess foundation twist. The Fluke 830 Laser Shaft Alignment Tool is another example of a high-precision laser alignment system.
- Key features of laser alignment tools include high accuracy (often to within 0.001 inches), real-time measurements, built-in tolerance checking, and intuitive user interfaces with step-by-step guidance. Many systems also offer cloud connectivity for easy data sharing and reporting.
- Prüftechnik offers a broad range of laser shaft alignment systems that adapt to virtually any asset, situation, or user skill level. Their systems are used in industries worldwide for high-precision, easy-to-use shaft alignment.
- Investing in laser alignment tools can significantly reduce maintenance costs by preventing equipment failures, unplanned downtime, and energy waste due to misalignment. Many suppliers offer ROI calculators to demonstrate the potential cost savings.
By leveraging laser alignment technology, millwrights can perform highly accurate shaft alignments in a fraction of the time required by traditional methods. This expertise is critical for ensuring the reliability, efficiency, and longevity of rotating machinery in industries ranging from manufacturing to power generation.
Optical Alignment Methods
Optical alignment methods are essential techniques used by millwrights to ensure precise positioning and alignment of industrial machinery components. These methods rely on the use of specialized optical tools and instruments to achieve high levels of accuracy and efficiency in the alignment process.

Here are some key optical alignment methods used by millwrights:
Collimation: This method involves using parallel light rays (collimated light) to align two telescopes or optical instruments. When the reticle of one telescope is illuminated, it projects collimated rays. By viewing these rays with a second telescope set at infinity focus and adjusting its aim until the cross-line images coincide, millwrights can ensure that the lines of sight of the two telescopes are parallel.
Auto-reflection: For precise angular accuracy, millwrights use the auto-reflection method. An optically flat mirror is mounted on the part to be positioned, with its reflecting surface parallel to the proper reference plane and in the line of sight of the alignment telescope. By turning and tilting the part until the reflected reticle image coincides with the actual reticle, millwrights can achieve accurate alignment.
Auto-collimation: Similar to auto-reflection, auto-collimation uses a mirror placed at an angle to reflect the image of the alignment telescope’s reticle back onto itself. This method allows for precise angular positioning of machinery components.
Laser alignment: Advanced laser alignment systems project a straight laser line or point to reference machinery positions. By measuring the deviation of the laser from the desired alignment points, millwrights can make precise adjustments to the machinery. Laser alignment is highly efficient and accurate, often achieving tolerances within 0.001 inches.
Optical micrometer: For applications requiring extreme precision, millwrights may use an optical micrometer. This instrument uses the principle of optical amplification to measure very small distances or movements, with resolutions down to 0.00001 inches. Optical micrometers are useful for aligning critical components in industries such as aerospace and semiconductor manufacturing.
In addition to these methods, millwrights must also consider factors such as line of sight, environmental influences, and the proper setup and calibration of optical instruments. Optical alignment requires a clear understanding of the principles involved and the ability to interpret and apply the measurement data effectively.
By mastering optical alignment methods, millwrights can ensure that industrial machinery is installed and maintained with the highest level of precision. This expertise is critical for optimizing equipment performance, reducing vibration and wear, and extending the lifespan of valuable assets across various industries.
Geometric Measurement Tools
Millwrights rely on a variety of geometric measurement tools to ensure the precise installation, alignment, and maintenance of industrial machinery. These tools enable millwrights to measure and correct geometric parameters such as straightness, flatness, squareness, plumb, and level, which are critical for optimal equipment performance and longevity.

Some of the key geometric measurement tools used by millwrights include:
- Laser alignment systems: Advanced laser alignment tools, such as the Easy-Laser E920, allow millwrights to perform quick and precise geometric measurements. These systems use laser transmitters and receivers to measure straightness, flatness, squareness, plumb, and level, providing highly accurate results and real-time adjustments.
- Straightness measuring tools: Millwrights use straightness measuring tools, such as the Easy-Laser E930, to measure the straightness and pointing direction of machine components like extruder pipes and hydraulic cylinders. These tools ensure that components are installed and aligned within strict tolerances to prevent vibration, wear, and premature failure.
- Flatness measurement systems: Flatness measurement tools, such as the Easy-Laser E910 and E915, are used by millwrights to measure the flatness of flanges, slewing bearings, and machine foundations. These systems use laser technology to provide precise measurements and help millwrights identify and correct any deviations from the desired flatness.
- Squareness measurement tools: Millwrights rely on squareness measurement tools to ensure that machine components are installed at precise right angles. The Easy-Laser E920 system, for example, can measure squareness in addition to other geometric parameters, allowing millwrights to verify and adjust the alignment of critical components.
- Plumb and level measurement tools: Plumb and level measurements are essential for ensuring that machinery is installed on a true vertical and horizontal plane. Millwrights use tools like the Easy-Laser E920 to measure plumb and level, as well as specialized laser levels and digital inclinometers, to achieve accurate alignment.
In addition to these specific tools, millwrights also use a range of precision measuring instruments, such as dial indicators, micrometers, and calipers, to verify dimensions and tolerances during the installation and maintenance process. By leveraging these geometric measurement tools and their expertise in precision alignment, millwrights can ensure that industrial machinery operates at peak efficiency, reliability, and longevity.
Advanced Machinery Diagnostics
Advanced machinery diagnostics is a crucial skill for millwrights, enabling them to identify and resolve complex issues in industrial equipment. This expertise helps optimize machinery performance, prevent costly downtime, and extend the lifespan of critical assets.
Millwrights use various advanced diagnostic techniques to assess the health and performance of rotating machinery, such as pumps, turbines, and compressors. These techniques include:
- Vibration analysis: By measuring and analyzing the vibration patterns of machinery, millwrights can detect issues like imbalance, misalignment, bearing wear, and gear mesh problems. Advanced vibration analysis tools, such as spectrum analyzers and phase analyzers, help pinpoint the root cause of vibration and guide targeted maintenance actions.
- Rotor dynamics: Understanding the dynamic behavior of rotating systems is essential for diagnosing and resolving complex machinery issues. Millwrights study rotor dynamics to analyze the effects of factors like mass distribution, stiffness, and damping on the vibration characteristics of machinery. This knowledge helps them identify and correct problems such as critical speed, instability, and excessive vibration.
- Thermography: Infrared thermography allows millwrights to detect temperature anomalies in machinery components, indicating potential issues like bearing failures, electrical faults, or insufficient lubrication. By identifying these problems early, millwrights can schedule maintenance interventions before catastrophic failures occur.
- Oil analysis: Analyzing lubricant samples from machinery can provide valuable insights into the condition of internal components. Millwrights use oil analysis to monitor wear rates, contaminant levels, and lubricant degradation, enabling them to optimize lubrication practices and prevent premature failures.
- Ultrasonic testing: Ultrasonic tools allow millwrights to detect leaks, assess the thickness of materials, and identify cracks or other discontinuities in machinery components. This non-destructive testing method helps evaluate the structural integrity of equipment and prevent failures due to material defects.
Advanced machinery diagnostics courses, such as those offered by Bently Nevada and other training providers, equip millwrights with the knowledge and skills needed to apply these techniques effectively. These courses cover topics like signal processing, data interpretation, fault diagnosis, and corrective action planning, enabling millwrights to tackle complex machinery issues with confidence.
By mastering advanced machinery diagnostics, millwrights can significantly improve the reliability, efficiency, and longevity of industrial equipment. This expertise is invaluable for industries that rely on critical machinery, as it helps minimize unplanned downtime, reduce maintenance costs, and ensure optimal performance.
Vibration Data Collection Methods
Vibration data collection is a crucial step in analyzing and addressing issues caused by machinery vibration. Millwrights use two primary methods for collecting vibration data: manual and automated.
In the manual method, trained personnel download routes from software on a computer onto a portable data collector. They then carry the data collector around the plant, collecting data from each designated location on the machines while they are under normal operating conditions. This is typically done at an average interval of once per month or quarter. After data collection, the device is connected to a computer and the routes are uploaded back into the software for analysis. This method relies heavily on manual involvement by skilled personnel to ensure an efficient process.

The automated method uses permanently mounted accelerometers on machines that are connected to data acquisition units. These units collect and process vibration data at designated intervals (every minute, hour, day, week, etc.) based on the criticality of the machine. This approach has a simplified layout with less personnel involvement in day-to-day operations. The collected data can be made available instantly online for all stakeholders to view.
Some key differences between manual and automated vibration data collection include:
- Manual method uses trained personnel, hardware, and software, while automated method uses a smart system of hardware and software.
- Manual data collection is usually done once a month on average, while automated collection can be as frequent as every minute depending on machine criticality.
- Manual method uses a handheld portable data collector, while automated method uses permanently mounted multi-channel data acquisition units.
- In manual collection, a single handheld accelerometer is moved between machines and data points, while automated collection uses permanently mounted accelerometers at each point.
- Manual collection data is available in software after performing a manual upload, while automated data is available automatically online using smart applications.
Effective vibration data collection, whether manual or automated, enables millwrights to make informed decisions about equipment health. By utilizing efficient data collection methods with permanently mounted accelerometers and centralized data storage, millwrights can develop optimized predictive maintenance programs. This allows them to identify faults without unnecessary intrusion, predict failures, and improve machinery reliability to reduce downtime.
Vibration Analysis Techniques
Vibration analysis is a crucial technique used by millwrights to assess the health and performance of industrial machinery. By measuring and interpreting vibration data, millwrights can detect potential issues, predict failures, and plan targeted maintenance actions.

Here are some key vibration analysis techniques used in the field:
- Spectrum analysis: This technique involves breaking down a vibration signal into its component frequencies using the Fast Fourier Transform (FFT) algorithm. By analyzing the frequency spectrum, millwrights can identify specific machine faults, such as unbalance, misalignment, bearing defects, and gear mesh issues. Spectrum analysis helps pinpoint the root cause of vibration problems and guides corrective actions.
- Time waveform analysis: Millwrights analyze vibration signals in the time domain to assess the overall health of machinery. Time waveform parameters, such as peak amplitude, root mean square (RMS) value, and crest factor, provide insights into the severity and nature of vibration. Changes in these parameters over time can indicate deteriorating machine condition and help predict potential failures.
- Phase analysis: Phase measurements reveal the relative timing of vibration signals from different points on a machine. Millwrights use phase analysis to diagnose problems like misalignment, bent shafts, and foundation issues. By comparing the phase relationships between vibration signals, they can determine the direction and extent of movement and make precise adjustments to correct the problem.
- Orbit analysis: This technique involves plotting the vibration motion of a rotor in a polar coordinate system. Orbit analysis helps millwrights visualize the dynamic behavior of rotating machinery and identify issues like rubs, instabilities, and fluid-induced vibrations. By analyzing orbit shapes and patterns, they can diagnose complex rotor dynamics problems and implement appropriate solutions.
- Envelope analysis: Also known as demodulation, envelope analysis is used to detect bearing faults and gear defects in the presence of background noise. This technique filters out low-frequency vibrations and amplifies high-frequency signals, making it easier to identify specific fault frequencies associated with bearing or gear damage. Envelope analysis enables early detection of these faults, allowing for timely maintenance interventions.
To perform these vibration analysis techniques, millwrights use specialized equipment such as accelerometers, data collectors, and analysis software. They must be proficient in sensor placement, data acquisition, signal processing, and interpretation of results. Millwrights also need to understand machine dynamics, failure modes, and maintenance practices to effectively apply vibration analysis in the field.
By leveraging these vibration analysis techniques, millwrights can accurately assess the condition of industrial machinery, identify potential problems, and take proactive measures to prevent failures and optimize performance. This expertise is essential for maintaining the reliability, efficiency, and longevity of critical equipment in various industries.
Frequency Analysis Techniques
Frequency analysis techniques are powerful tools used by millwrights to analyze vibration data and diagnose machinery faults. These techniques involve decomposing vibration signals into their constituent frequencies and amplitudes, allowing millwrights to identify specific machine components and failure modes. Some key frequency analysis techniques include:
Fast Fourier Transform (FFT): FFT is a mathematical algorithm that converts time-domain vibration data into the frequency domain. It breaks down a complex vibration signal into a series of discrete frequency components, each with its own amplitude. By analyzing the FFT spectrum, millwrights can identify dominant frequencies and their associated machine components, such as shafts, bearings, gears, and blades.
Order analysis: Order analysis is a technique used to analyze vibration signals from rotating machinery. It involves resampling the time-domain data at equal angular increments, rather than equal time increments, to account for variations in rotational speed. This allows millwrights to identify vibration components that are synchronous with the machine’s rotation, such as unbalance, misalignment, and blade pass frequencies.
Envelope analysis: Envelope analysis, also known as demodulation, is a technique used to detect bearing and gear faults in the presence of background noise. It involves filtering out low-frequency vibrations and extracting the high-frequency envelope signal, which contains fault-specific impact frequencies. By analyzing the envelope spectrum, millwrights can identify characteristic fault frequencies associated with bearing and gear damage, such as ball pass frequencies and gear mesh frequencies.
Time synchronous averaging (TSA): TSA is a technique used to extract periodic waveforms from noisy vibration signals. It involves dividing the signal into segments of equal length, each corresponding to one rotation of the machine, and averaging these segments together. This process reduces non-synchronous noise and enhances the periodic components of the signal, making it easier to identify faults such as gear tooth damage, blade cracks, and rotor bar failures.
Cepstrum analysis: Cepstrum analysis is a technique used to detect harmonics and sidebands in vibration spectra. It involves calculating the inverse FFT of the logarithm of the power spectrum, resulting in a “spectrum of a spectrum.” Cepstrum analysis is particularly useful for identifying families of equally spaced frequency components, such as those associated with gearbox faults and bearing inner race defects.
By applying these frequency analysis techniques, millwrights can extract valuable diagnostic information from complex vibration signals. This enables them to identify specific machine faults, assess their severity, and plan targeted maintenance actions to prevent failures and optimize equipment performance. Frequency analysis is a core skill for millwrights working in predictive maintenance and condition monitoring roles across various industries.
Thermal Growth Compensation
Thermal growth compensation is a critical technique used by millwrights to account for the expansion or contraction of machinery components due to temperature changes. This is essential for maintaining proper alignment and preventing issues caused by thermal growth.
During normal operation, machinery is influenced by various factors, including temperature changes, which can cause the height of shafts to increase. This phenomenon is known as thermal growth. To compensate for this, millwrights enter offset and angle values based on a calculation point, which is either the center of the coupling for short flex or the left side of the spacer for spacer shafts.

Millwrights use specialized tools and software to calculate and apply thermal growth compensation values. For example, the Easy-Laser XT770 alignment system allows users to enter vertical and horizontal compensation values for the coupling or feet. The software then adjusts the alignment targets to account for the expected thermal growth, ensuring that the machinery will be properly aligned when it reaches its operating temperature.
It is important to note that thermal growth compensation cannot be applied to both the coupling and feet on the same machine. Millwrights must choose one or the other based on the specific machinery and application.
In addition to shaft alignment, thermal expansion compensation is also crucial for other aspects of industrial machinery. Accumulators, for example, are used to prevent lines, pipes, and seals from rupturing due to the thermal expansion of fluids in hard-plumbed systems. By properly sizing and installing accumulators, millwrights can safely accommodate the increased fluid volume caused by heat.
Thermal growth compensation algorithms are another tool used by millwrights to predict and correct for thermal deformation in machine tools. These algorithms, developed through testing and finite element analysis (FEA), help improve the accuracy and performance of machine tools subject to thermal influences.
In summary, thermal growth compensation is a vital skill for millwrights working with industrial machinery. By accurately accounting for thermal expansion and contraction, they can ensure proper alignment, prevent damage, and optimize equipment performance under varying temperature conditions. This expertise is essential for maintaining the reliability and longevity of critical assets in industries worldwide.
Safety Protocols and Standards
Millwrights adhere to strict safety protocols and standards to protect themselves and others on the job site. Safety is a top priority, as they often work with heavy machinery, high-voltage equipment, and in hazardous environments.
Some key safety protocols and standards followed by millwrights include:
- Lockout/Tagout (LOTO) procedures: Before performing maintenance or repairs on machinery, millwrights must follow LOTO procedures to ensure that equipment is properly shut down and cannot be started up accidentally. This involves locking and tagging energy isolation devices, such as electrical breakers or valves, to prevent unexpected startup or release of stored energy.
- Personal Protective Equipment (PPE): Millwrights must wear appropriate PPE, such as hard hats, safety glasses, steel-toed boots, gloves, and hearing protection, to minimize the risk of injuries from falling objects, flying debris, loud noises, and other hazards.
- Fall protection: When working at heights, millwrights use fall arrest systems, such as harnesses and lanyards, to prevent serious injuries in case of a fall. They also follow proper procedures for using ladders, scaffolds, and lift equipment to access elevated work areas safely.
- Hazard communication: Millwrights must be familiar with the Globally Harmonized System (GHS) for classifying and labeling hazardous chemicals. They must know how to read and interpret Safety Data Sheets (SDS) to understand the risks associated with the substances they work with and take appropriate precautions.
- Confined space entry: When working in confined spaces, such as tanks, vessels, or pipelines, millwrights follow strict protocols to ensure adequate ventilation, monitor atmospheric hazards, and maintain communication with a standby person outside the space.
- Regular safety training: Millwrights participate in ongoing safety training to stay current with industry standards, best practices, and emerging hazards. This includes OSHA-mandated training, such as the OSHA 10-hour or 30-hour courses, as well as job-specific training provided by employers or unions.
By adhering to these safety protocols and standards, millwrights not only protect themselves but also contribute to a safer work environment for everyone on the job site. Their commitment to safety helps prevent accidents, minimize downtime, and ensure the smooth operation of industrial facilities.
Modern Millwright Training Programs
Modern millwright training programs equip aspiring millwrights with the diverse skills and knowledge needed to excel in this dynamic field. These programs typically involve a combination of classroom instruction and hands-on training to ensure that students gain both theoretical understanding and practical experience.
Apprenticeship programs are the most common pathway for becoming a millwright. These programs usually last 3-5 years and include a minimum of 1,560 hours of on-the-job training annually under the guidance of experienced millwrights. Apprentices learn essential skills such as machinery installation, maintenance, repair, and precision alignment while working on real projects.
Classroom instruction is another crucial component of millwright training. Students learn about various topics, including mechanical systems, hydraulics, pneumatics, welding, and machine shop practices. They also study subjects like math, blueprint reading, and safety protocols to develop a well-rounded understanding of the trade.
Some of the key skills covered in modern millwright training programs include:
- Welding: Students learn different welding techniques, such as MIG, TIG, and arc welding, which are essential for fabricating and repairing industrial machinery.
- Precision alignment: Trainees learn how to use advanced alignment tools, like laser alignment systems and dial indicators, to ensure that machinery components are installed and maintained within precise tolerances.
- Mechanical and electrical systems: Students gain knowledge of various mechanical and electrical systems, including hydraulics, pneumatics, and programmable logic controllers (PLCs), which are commonly found in industrial settings.
- Rigging and hoisting: Apprentices learn how to safely use rigging and hoisting equipment to move and position heavy machinery during installation and maintenance.
Many training programs also incorporate cutting-edge technologies, such as 3D printing and robotics, to familiarize students with the latest advancements in the field. This ensures that millwrights are well-prepared to work with modern industrial equipment and adapt to evolving industry practices.
Upon completion of their training, millwrights must pass a comprehensive exam to earn their professional certification, such as the Red Seal certification in Canada. This certification demonstrates their competence and adherence to industry standards, making them highly sought-after by employers across various sectors.
Continuous learning is also emphasized in the millwright profession, with many pursuing additional training in specialized areas like vibration analysis, thermography, and predictive maintenance to further enhance their expertise and stay current with emerging technologies.
In summary, modern millwright training programs provide a comprehensive education that combines theoretical knowledge with practical skills, ensuring that graduates are well-equipped to tackle the complex challenges of installing, maintaining, and repairing industrial machinery in today’s ever-evolving industrial landscape.
More useful info you can find 👉 here 👈